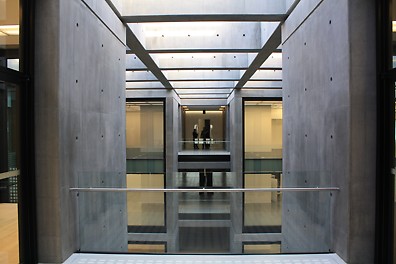
Beautiful exposed concrete is possible with PERI
The placement and number of tie points have a big impact on appearanceFormwork diagram for MAXIMO (left) & TRIO (right) showing the requirement to fill unusued tie points before concreting works, whilst also considering the improved visual appearance from centralised tie points where possible.
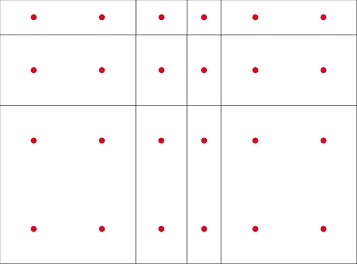
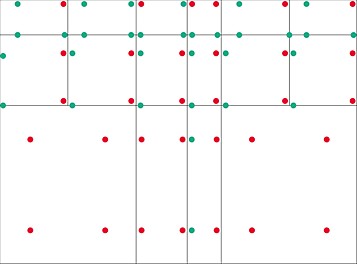
Occupied anchor points are marked red. Anchor points marked in green are not occupied and must be sealed before concreting.
Function of the anchor closure technology
The type of installation of the formwork anchors is crucial when dealing with anchor holes. As a rule, the reusable anchor rod is pushed through a cladding tube made of fiber concrete or plastic that is permanently installed in the concrete and is closed on both sides with conically tapered plastic moldings that can be removed again after the formwork has been removed.
The resulting openings are then closed using sealing cones or sealing plugs. Plastic plugs are generally used in standard versions. In other cases, the cladding pipes are closed with cones made of fiber concrete.
In some cases, the anchor rod is embedded in concrete. For this purpose a steel/plastic sealing cone is screwed onto the anchor rod before concreting, which is also removed again after the formwork has been removed.
These anchor points then usually have to be closed with fiber concrete cones. What matters most is the later function of the wall. The closure of anchor holes in more demanding applications such as requirements for drinking water, groundwater, or fire and noise protection requires higher quality and usually a test report as proof. The highest, albeit different requirements for closure technology are ultimately placed on walls made of waterproof concrete and in exposed concrete.
We can provide a solution for any of these applications, and help to advise how to meet any specifications you must adhere to on your next project.
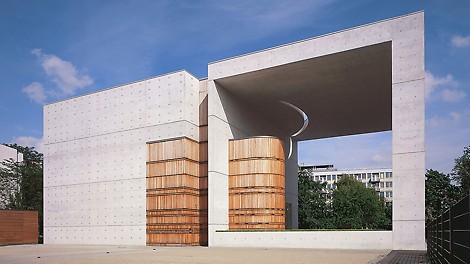
Anchor closure technology for exposed concrete
The surface design of concrete includes the texture of the formlining, the colour of the concrete and the arrangement of the formwork elements. But the individual parts of the tensioning sets of the formwork anchors are also effective design details that can be controlled through variations in the closure geometry as well as through the choice of material for the cones and plugs.
In the PERI MAXIMO frame formwork with one-sided anchor technology, all anchors are arranged in the middle of the element. For this purpose, exposed concrete anchor points can be created using the standard MX anchor, which are visibly closed with either plastic plugs, screw plugs made of plastic/stainless steel or glued-in fiber cement plugs. If there are special optical requirements, anchoring can also be done using magnetic cones. The magnets inserted in the cone fix it securely on the metal ring of the seal built into the formwork element. The magnets must always rest directly on the seal of the element. The negative openings of the magnetic cones are subsequently covered with DK concrete cones in the “flush, recessed or with shadow gap” variants. This application is popular for non-residential buildings such as schools, offices and swimming pools, etc.
For double-sided anchoring with a cladding tube and sealing cone, the sealing cones should be equipped with a lip seal or an additional foam rubber seal due to the anchor expansion that occurs during concreting. This means that a sharp-edged design can be achieved without the finest parts being run out. Depending on the design requirements, the anchor points can also be created using the silhouette cone (shadow gap), the recessed or flush concrete cone.
Design example of anchor points
There are different solutions for different architectural requirements.
Anchor closure technology for waterproof concrete
In buildings made of waterproof concrete, the concrete as a rigid seal not only has structural load-bearing tasks, but also sealing functions. Waterproof concrete is mostly used for foundation components, basement walls and water tanks.
The conventional methods of making anchor points watertight are not reliable in practice. As the concrete hardens, shrinkage cracks form, which may run along the entire wall thickness along the tie point. Difficulties also arise during the formwork stripping process. Construction processes often require that the formwork has to be removed just one day after concreting. The anchor nut of the tension point is loosened with several blows of the hammer. The impact can shake anchor rods and built-in parts. The result is hairline cracks that over time develop as weak points and as routes for fluids to penetrate the structure.
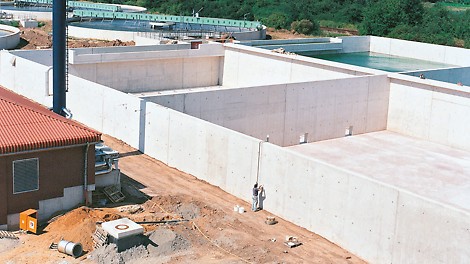
In order to seal tension points, careful work is required, regardless of the method. With its DK and SK anchor systems, we have developed two technical solutions for subsequently sealing the tie points. They are impermeable to water and gas, fire-resistant as well as sound-absorbing and diffusion-tight.
The anchor points are closed here with glued-in DK concrete cones. Cone and spacer tubes are available for different anchor diameters. This means that the chance of creating tight walls is much greater than with conventional applications. Depending on the requirements, test reports are also available, which are usually requested by either the customer or the client.
The SK system consists of two reusable SK anchor cones and 3 anchor rods, of which the middle one can be embedded in concrete (e.g. in security wings and radiation structures). For all other applications, a cladding tube is used so that the middle tension rod can be reused. The closure with the sealing cover DW15, 20 and 26 is analogous to handling with the DK sealing system. The SK anchor cones are suitable for water-impermeable, fire-resistant, sound-absorbing and radiation-proof anchor points.
The DK system consists of two reusable sealing cones (DK) and a concrete-encased spacer tube. The sealing cover between the cone and the formwork compensates for unevenness and prevents the ingress of concrete. All three available sealing cones DW15, DW20 and DW26 as well as MAXIMO (without spacer tube, but with magnetic cone) have the same external shape so that a DK concrete cone fits into all cone openings.
For MAXIMO with the conical one-sided MX anchor technology, the anchor points are usually made with the screw plugs MX15/50, MX15/75, MX18/75. Test reports are also available for these closure technologies.
Structure and application of PERI sealing cones
System DK sealing conesThe system consists of two reusable DK sealing cones and a concrete-encased spacer tube. The sealing cover DW15 between the cone and the formwork overcomes unevenness and prevents the ingress of concrete fluids.
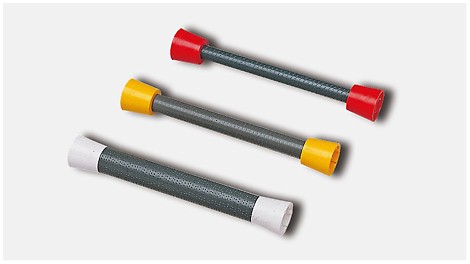
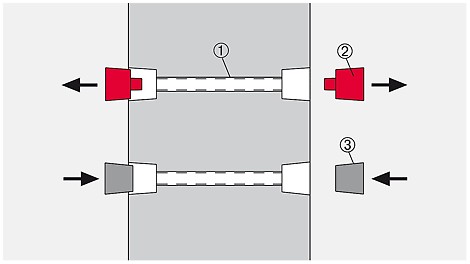
1 = pipe rough (1x)
2 = DK sealing cone (2x)
3 = DK concrete cone (2x)
The SK system consists of two reusable anchor cones (SK) and three anchor rods, of which the middle one can be embedded in concrete, for example in security wings and radiation structures. The closure is easily completed with the sealing cover DW15, DW20 or DW26.
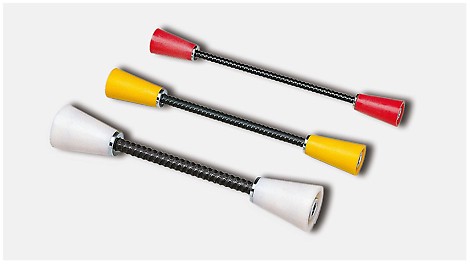
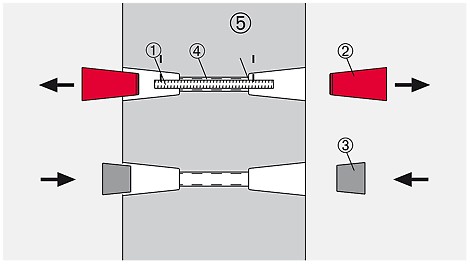
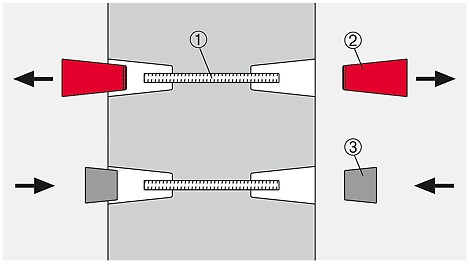
System SK sealing cones - tension rod recoverable:
1 = Recoverable tension rod (1x)
2 = SK anchor cone (2x)
3 = SK concrete cone (2x)
4 = pipe rough (1x)
5 = SK pipe seal (2x)
System SK sealing cones - tension rod lost:
1 = tension rod lost (1x)
2 = SK anchor cone (2x)
3 = SK concrete cone (2x)